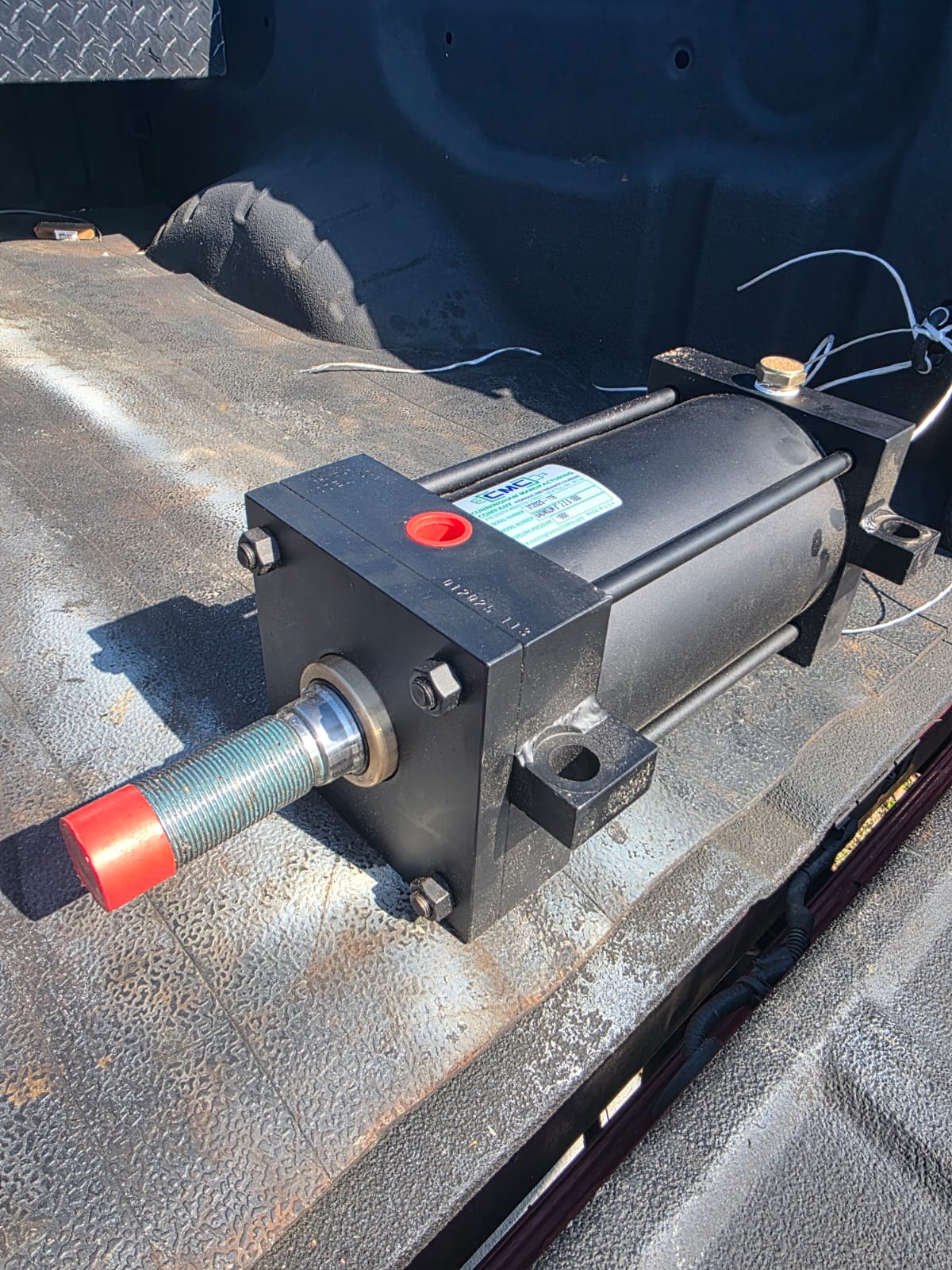
Jerry Showalter
July 15, 2022
15 min read
Essential Preventive Maintenance Checklist for Hydraulic Systems
preventive maintenancemaintenance checklistsystem inspectionhydraulic maintenancepreventive measures
Essential Preventive Maintenance Checklist for Hydraulic Systems
Introduction
Preventive maintenance is crucial for maintaining the reliability and efficiency of hydraulic systems. This comprehensive checklist provides detailed guidance for daily, weekly, monthly, and annual maintenance procedures to ensure optimal system performance and prevent costly breakdowns.
Daily Maintenance Tasks
1. Visual Inspections
- Check fluid levels in reservoirs and maintain proper levels
- Inspect for visible leaks around fittings, seals, and hoses
- Monitor system pressure gauges and compare with normal operating ranges
- Check temperature indicators and ensure proper operating temperature
- Observe system operation for unusual noise or vibration
2. Performance Monitoring
- Record operating pressures at key points
- Monitor system temperature during operation
- Check flow rates if flow meters are installed
- Observe actuator movement for smooth operation
- Document any deviations from normal operation
3. Basic Cleaning
- Clean visible dirt and debris from components
- Wipe down external surfaces
- Clear any obstructions from cooler fins
- Clean sight glasses for proper level monitoring
- Remove any accumulated debris around moving parts
Weekly Maintenance Procedures
1. Filter Maintenance
- Check filter condition indicators
- Record pressure drops across filters
- Clean or replace filter elements as needed
- Inspect breather caps and clean as necessary
- Verify proper filter seating and housing integrity
2. System Checks
- Test accumulator pre-charge pressure
- Check belt tensions on pumps and motors
- Inspect coupling alignments
- Verify relief valve settings
- Test system safety interlocks
3. Component Inspection
- Check pump and motor shaft seals
- Inspect cylinder rod conditions
- Examine hose conditions and routing
- Verify secure mounting of all components
- Check electrical connections and controls
Monthly Maintenance Tasks
1. Fluid Analysis
- Take oil samples for laboratory analysis
- Check fluid cleanliness levels
- Test fluid viscosity
- Measure acid number
- Monitor water content
- Record metallic particle content
2. Detailed Component Inspection
- Conduct thorough pump inspection
- Check valve operation and settings
- Inspect cylinder cushions and seals
- Examine heat exchanger efficiency
- Test electrical and electronic controls
3. System Performance Analysis
- Record and trend system pressures
- Measure and document flow rates
- Check system response times
- Verify sequence operations
- Test emergency systems
Quarterly Maintenance
1. Comprehensive Testing
- Conduct full system pressure tests
- Perform flow analysis at all ports
- Check all pressure settings
- Test all safety devices
- Verify control system functions
2. Advanced Diagnostics
- Perform vibration analysis
- Conduct thermographic scanning
- Test oil cleanliness
- Check alignment of all components
- Verify calibration of all sensors
Annual Maintenance
1. Major System Inspection
- Complete system teardown as needed
- Replace all filters
- Change hydraulic fluid
- Clean reservoir thoroughly
- Inspect all internal components
2. Component Overhaul
- Rebuild or replace pumps as needed
- Service all valves
- Replace seals and bearings
- Overhaul cylinders
- Update control systems
Documentation and Record Keeping
1. Maintenance Records
- Document all maintenance activities
- Record component replacements
- Keep fluid analysis reports
- Maintain pressure and temperature logs
- Track system modifications
2. Performance Trending
- Monitor system efficiency
- Track energy consumption
- Record component life cycles
- Document failure patterns
- Analyze maintenance costs
Emergency Procedures
1. Breakdown Response
- Emergency shutdown procedures
- Troubleshooting guidelines
- Spare parts inventory
- Emergency contact information
- Recovery procedures
2. Safety Considerations
- Personal protective equipment requirements
- Lock-out/tag-out procedures
- Fluid handling safety
- Emergency cleanup procedures
- First aid protocols
Preventive Maintenance Best Practices
1. Training Requirements
- Operator training
- Maintenance staff certification
- Safety training
- Documentation procedures
- Emergency response training
2. Tools and Equipment
- Required maintenance tools
- Diagnostic equipment
- Cleaning supplies
- Safety equipment
- Calibration tools
Conclusion
Following this comprehensive preventive maintenance checklist will help ensure:
- Extended system life
- Reduced downtime
- Improved reliability
- Lower operating costs
- Enhanced safety
Regular maintenance is an investment in your hydraulic system's future performance and reliability. Implement these procedures consistently and maintain detailed records for optimal results.
Additional Resources
- Manufacturer specifications
- Industry standards
- Training materials
- Technical support contacts
- Emergency service providers