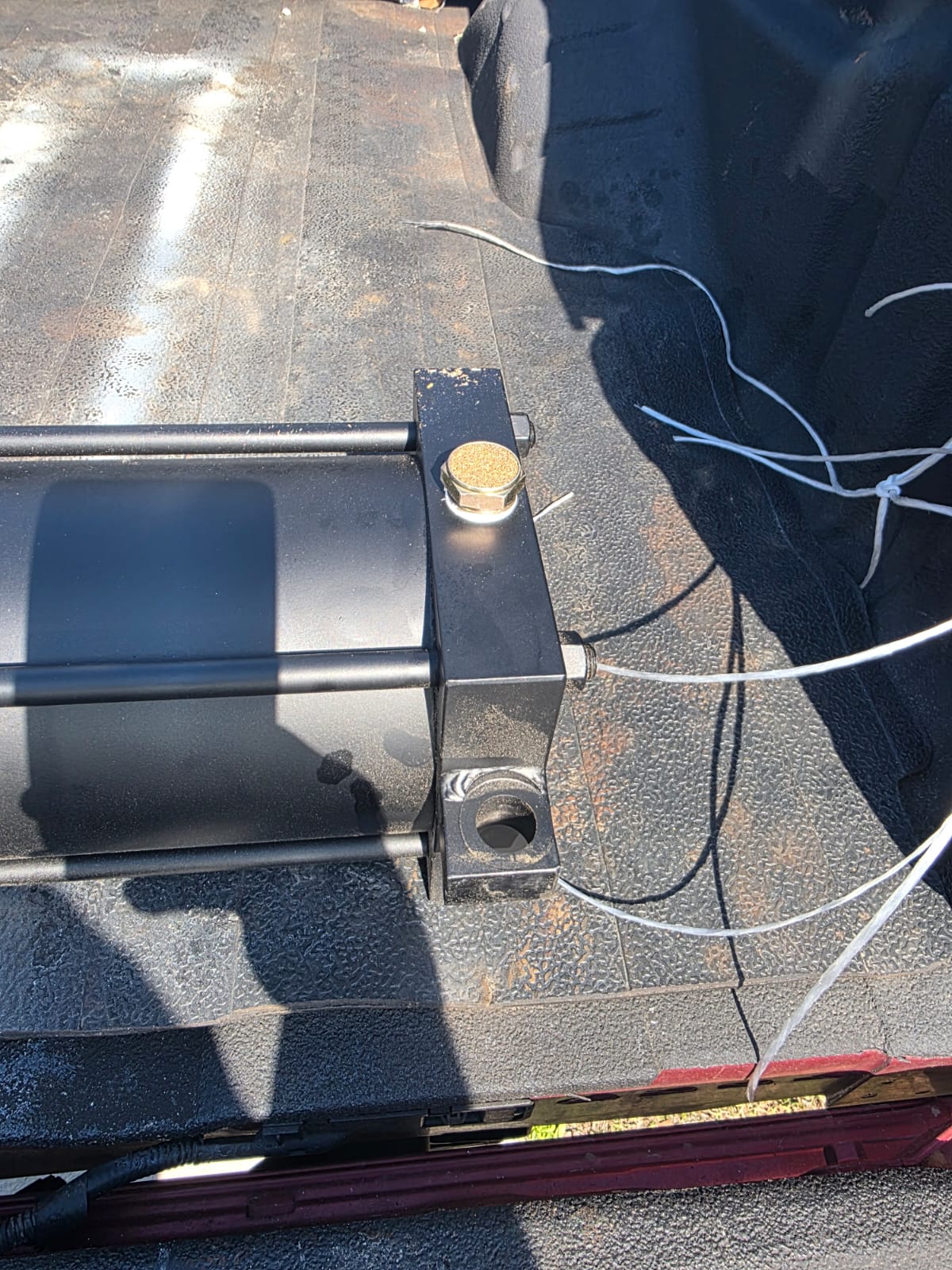
Understanding Hydraulic System Maintenance: A Comprehensive Guide
Understanding Hydraulic System Maintenance: A Comprehensive Guide
Introduction to Hydraulic System Maintenance
Proper maintenance of hydraulic systems is crucial for ensuring optimal performance, reliability, and longevity of industrial equipment. This comprehensive guide explores the essential aspects of hydraulic system maintenance, from routine checks to advanced preventive measures.
The Importance of Regular Maintenance
Regular maintenance is the cornerstone of hydraulic system reliability. Studies show that properly maintained hydraulic systems can operate at peak efficiency for 10-15 years, while poorly maintained systems may fail within 2-3 years. This significant difference in service life demonstrates the critical nature of proper maintenance procedures.
Key Components Requiring Regular Attention
1. Hydraulic Fluid Management
- Regular fluid analysis (every 500 operating hours)
- Contamination monitoring and control
- Temperature monitoring (optimal range: 100-140°F)
- Viscosity testing and maintenance
- Water content monitoring (should be less than 0.1%)
2. Filtration System Maintenance
- Return line filter inspection
- Pressure filter monitoring
- Breather filter replacement
- Filter element analysis
- Bypass valve inspection
3. Component-Specific Maintenance
Pumps and Motors
- Pressure and flow testing
- Efficiency monitoring
- Seal inspection and replacement
- Bearing condition assessment
- Shaft alignment verification
Cylinders and Actuators
- Rod inspection for scoring
- Seal condition assessment
- Mounting bolt torque checks
- Cushion adjustment verification
- Position sensor calibration
Preventive Maintenance Strategies
1. Scheduled Inspections
- Daily visual checks
- Weekly performance monitoring
- Monthly system analysis
- Quarterly comprehensive evaluation
- Annual overhaul assessment
2. Predictive Maintenance Techniques
- Vibration analysis
- Thermal imaging
- Oil analysis trending
- Pressure decay testing
- Flow rate monitoring
Troubleshooting Common Issues
1. System Performance Problems
- Slow operation
- Erratic movement
- Excessive noise
- High fluid temperature
- Poor response time
2. Component-Specific Issues
- Pump cavitation
- Cylinder drift
- Valve malfunction
- Seal failure
- Accumulator problems
Best Practices for System Longevity
1. Documentation and Record Keeping
- Maintenance logs
- Performance trending
- Repair history
- Component replacement tracking
- Oil analysis results
2. Training and Expertise
- Operator training
- Maintenance staff certification
- Safety procedures
- Emergency response protocols
- Continuous education
Advanced Maintenance Considerations
1. Environmental Factors
- Temperature control
- Contamination prevention
- Humidity management
- Ventilation requirements
- Storage conditions
2. System Optimization
- Energy efficiency
- Performance monitoring
- Load analysis
- Circuit optimization
- Control system tuning
Conclusion
Effective hydraulic system maintenance requires a comprehensive approach combining regular inspection, preventive measures, and proper documentation. By following these guidelines, organizations can significantly extend their hydraulic systems' life while maintaining optimal performance and reliability.
Additional Resources
- Industry standards and specifications
- Manufacturer recommendations
- Training programs
- Technical support
- Emergency services